Motorcycle head pipe process equipment| CNC double-end head pipe expansion machine| Made in Taiwan
In the processing of metal pipe fittings, the traditional hydraulic press is mostly designed in three directions, that is, the deformation of the workpiece in three directions is controlled by the hydraulic system. However, the HC-6606 double-end expansion and shrinking machine developed by HoChier Taiwan not only has the ability of double-end expansion and shrinking, but also has the function of puncher auto shift which is an exclusive design that is rare in the market at present.
What exactly are the advantages of auto shfit puncher technology?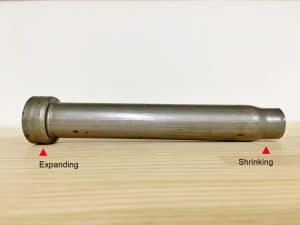
-
Higher processing flexibility
While the HC-6606 has a built-in automatic mold displacement system,
the HC-6606 can move puncher during the machining process without the need to replace or manually adjust the mold, greatly improving production efficiency. -
Pre-forming and final forming in one go
Conventional molding equipment may require multiple processes to complete the forming of the workpiece, but this model uses automatic puncher shift to complete the pre-forming and final molding in the same station, which not only reduces the number of steps, but also ensures the machining accuracy. -
Improve consistency and stability
Through numerical control of puncher shift, to ensure the accuracy of each processing, reduce the error of manual intervention, so that each workpiece can achieve the same specifications and quality. -
Reduce mold wear and extend service life
Because the puncher can move the position , it avoids the eccentric wear or excessive stress that may occur in the fixed mold, further prolongs the life of the mold and reduces the production cost.
Technology application and industrial value
HC-6606 double-ended pipe expansion and shrinking machine is suitable for the processing of metal pipe fittings such as motorcycle frame head pipe, faucet tube, shock absorber tube, exhaust pipe, seat bracket, etc., especially suitable for motorcycle, bicycle, automobile and motorcycle parts manufacturing industry. This machine has been adopted by several Yamaha T1 suppliers, demonstrating its reliability and competitiveness in the industry.
This innovative mold displacement technology not only improves machining accuracy, but also makes metal tube forming faster, more stable and more cost-effective, making it an indispensable solution for modern manufacturing.